The sustainability of plastic packaging is increasingly determined by its recyclability. Circular economy is the megatrend. Polyethylene terephthalate (PET) is the world’s most recycled plastic and is ideal for packaging food. Building on this knowledge, Sukano and Illig have launched an initiative to enable the use of PET in cups and trays for microwave and hot fill applications. The result is a possible alternative to the PS and PP applications that are often used today but that are either unsuitable for recycling or are not food compliant.
Crystalline and opaque CPET variants, such as CPET trays that are heat-resistant up to 220 °C, are currently used for temperature-resistant applications. Conventional thermoformed APET cups and trays do not reach the lower – and usually only briefly reached – temperature threshold of 100 °C, which is typical for microwave applications and hot filling. Therefore, the high-temperature-resistant CPET does not necessarily have to be used as a packaging material either. The Swiss additive and master batch specialist Sukano and the German thermoforming systems manufacturer Illig have developed a new material for this purpose.
CPET-Light Closes the Gap
The two companies have developed the temperature-resistant CPET-light based on CPET thermoforming technology. The goals here were to realize a transparent application for use in microwaves and for hot filling while simultaneously increasing the productivity of the selected thermoforming system.
For this project, Illig developed a more efficient thermoforming process that delivers improved productivity compared to conventional CPET. It involves producing CPET-light cups by means of precise temperature control of the film nucleated with the Sukano master batch and a specially developed tool. These cups offer the benefit of being suitable for reuse as food packaging in the PET raw material cycle and therefore offer an alternative to PS and PP.
Production of Transparent Cups for Hot Filling
The joint project aimed to produce hot-fillable cups for dairy products that have sufficient transparency and a temperature resistance of 100 °C. In this series of tests, an RDM 70K thermoforming machine and a single-cavity mold were used at the Illig Technology Center. An identical molding tool was used to produce samples from PP-H and APET as a reference. For the test series, the master batch specialist produced both transparent and white CPET-light films with a thickness of 1.1 mm and a width of 240 mm on the laboratory extruder in its in-house Technology Center. This resulted in a test series with PP-H, APET, CPET-light (white) and CPET-light (transparent).
The cycle rate for the cups made of CPET-light was optimized during the thermoforming tests. The maximum cycle rate achieved during the process was 20 cycles/min. The cups made of PP-H and APET were also produced with 20 cycles/min. It was important to achieve comparable wall thickness distributions in order to obtain meaningful results for the optical and mechanical tests.
The following investigations were carried out:
- Wall thickness measurement of the cups at characteristic points after 24 h of storage
- Determination of tool shrinkage after 24 h of storage
- Top load measurement of the formed cups Temperature resistance in the oven test
- Temperature resistance with hot water
- Transparency measurement
The measurements of the wall thickness clearly showed that, with the exception of the APET cups (bottom too thinly formed) and the white CPET-light cups (tear-off under the sealing rim), the wall thickness distributions achieved in the thermoforming process were very comparable. This made it possible to draw meaningful conclusions from the top-load measurements. Five cups each were tested with the Magna Mike 8600 Hall Effect thickness gauge.
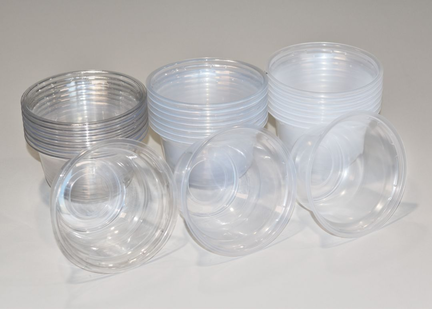
Determination of Tool Shrinkage after 24 h of Storage
Preliminary tests had already indicated that the tool shrinkage of APET and CPET-light were comparable. They corresponded to the values of approx. 0.5 % known in tool design. The shrinkage value of 1.58 % for PP was also within the tolerance range. There was a tendency for the shrinkage values determined for APET, CPET-light and PP to be slightly lower, which was due to the tempering in the heated mold. The diameter of five cups was measured optically for each film material and compared with that of the die contour.
Upset pressure measurements of the formed cups were also carried out (top-load measurements). A Zwick/Roell zwickiLine 2.5 kN and two plane-parallel compression plate dies were used for this purpose. The test method was based on the DIN 55440 compression test.
10 cups were tested per test point. The following became apparent when considering the maximum force values (Fmax) from the tests: The lower wall thickness of the white CPET-light cups below the sealing rim had a negative effect on the maximum compression force of the cups. This could also be observed during the test in the form of an earlier onset of deformation. The APET cups with their thinner wall thickness in the bottom showed a similar behavior with an earlier deformation and lower Fmax value. When comparing the PP cups with the transparent CPET-light moldings, a clear difference in the Fmax values was observed, which can be attributed to the differences in the Young's modulus of PP (approx. 2000 MPa) and PET (approx. 3800 MPa).
Temperature Resistance in the Oven Test
The cup samples were exposed to 100 °C for 30 minutes in the oven test. Subsequently, the shrinkage values were checked visually by measuring the cup diameters at the sealing rim.
The APET cups could no longer be measured due to the massive deformation. The decrease in cup height was smallest for the PP cups. However, deformation of the CPET-light samples was further reduced by optimization of the tool geometry.
The cups were filled to the brim with approx. 95 °C hot water. After one minute the water was emptied and after another 30 minutes the cup dimensions were measured. The transparency was measured with a haze meter – Hazegard plus from BYK Gardner – according to ASTM D-1003. Here, the transparent CPET-light cup showed only a slight increase in Haze values compared to the APET cup. An optical inspection of CPET-light transparent and PP revealed that they could be considered visually equivalent.
CPET-Light Cups as an Efficient and Recyclable Alternative
The combination of the film nucleated with the Sukano master batch, the appropriate molding tool, thermoforming machinery and the two companies’ many years of know-how have led to the successful development of a CPET-light cup with a temperature resistance of up to 100 °C. The good barrier properties of PET also ensure that the cups are grease-resistant. Efficient production is also ensured due to the machine speed of up to 20 cycles/minute.
The transparent variant, which includes additives from the specially formulated nucleation master batch from the Swiss specialist Sukano, also offers a possible alternative to the PP cups that are frequently used today. PET's excellent recyclability, especially for food-compliant recycling, can make a significant contribution to a successful circular economy.
What is CPET-Light?
- Thermoformed, partially crystalline application made of PET
- Available as opaque and transparent application
- Temperature-resistant up to 100 °C thanks to formulated additives and a special processing method
- Suitable for use in microwaves and hot filling
- Recyclable
- Good barrier properties thanks to PET